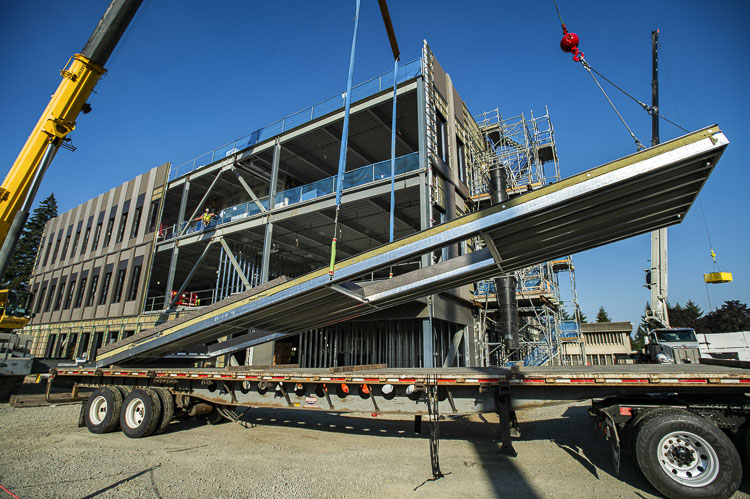
Progressive design-build project delivery method streamlines use of prefab, eliminates two months from timeline and saves more than $1 million overall
VANCOUVER – Mortenson, a leading developer and design-builder in Oregon, along with Portland-based Opsis Architecture, California-based DGA Architects, and Wilsonville-based contractor and fabricator Western Partitions, Inc., completed installation in late October of a prefabricated building enclosure system on the Bonneville Power Administration (BPA) Ross Complex Technical Services Building in Vancouver. The progressive design-build project delivery method being used for the project streamlined the use of prefabrication, reduced two months from the construction timeline and gleaned a savings of more than $1 million on the overall budget.
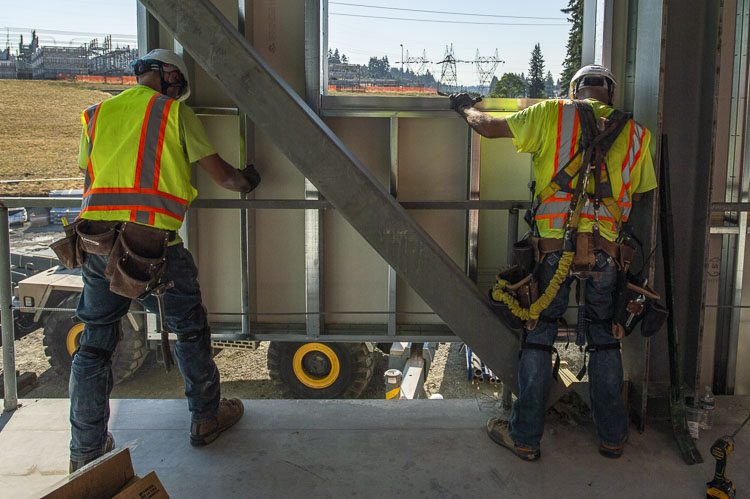
According to BPA, the new facility will help avoid $25 million in upgrades to the old buildings it is replacing, and help save hundreds of thousands of dollars per year in avoided lease costs. A critical component of BPA’s operations, the Technical Services Building will support maintenance, testing and repair to maintain modern electronic transmission communications and controls. The Technical Services Building project is scheduled for completion the summer of 2023.
While prefabrication is not a new solution for efficiency in commercial construction, the use of prefabricated panels on a building exterior is still quite rare. The key to the successful use of prefabrication for the Technical Services Building is the progressive design-build delivery method being used to construct this building. Heralded by the Design-Build Institute of America, this method prescribes that the design-builder is selected by the owner early in the project and primarily for their qualifications. As with all progressive design-build projects, the Technical Services Building is being delivered in two distinct phases: design development and pre-construction, and final design and construction.
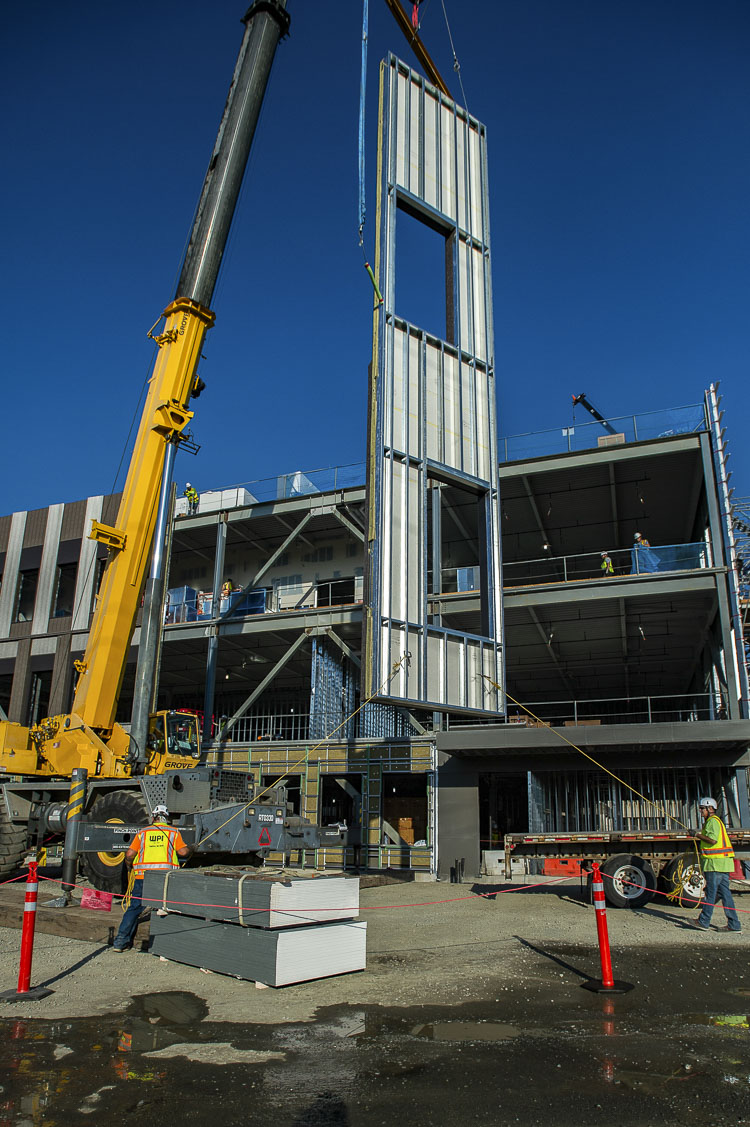
“Progressive design-build delivery lends to the use of prefabrication and its related benefits, including the early selection of materials and associated cost efficiencies. We consider the Technical Services Building project a template for progressive design-build teams seeking to optimize value and design of a whole project from the beginning through to project delivery,” says Trent Rehfeldt, Mortenson market executive. “Prefabrication is also a creative approach for offsetting increasing materials costs and the craft worker labor shortage the construction industry is facing.”
As part of the pre-construction planning process, the design-build team explored ways for maximizing their respective strengths to provide the greatest value possible, resulting in an early decision to use prefabrication. After evaluating seven types of enclosure systems, the team opted to leverage Western Partition’s ability to fabricate the façade panels at its facility less than 10 miles from the project site.
“This project brought unique challenges that we haven’t had to address before,” says Kim Lindman, Western Partitions, Inc., project manager. “It changed our approach to be able to maximize the architectural design we were seeking. That’s the fun part of prefab – stepping out of the box and figuring out how we’re going to make it work.”
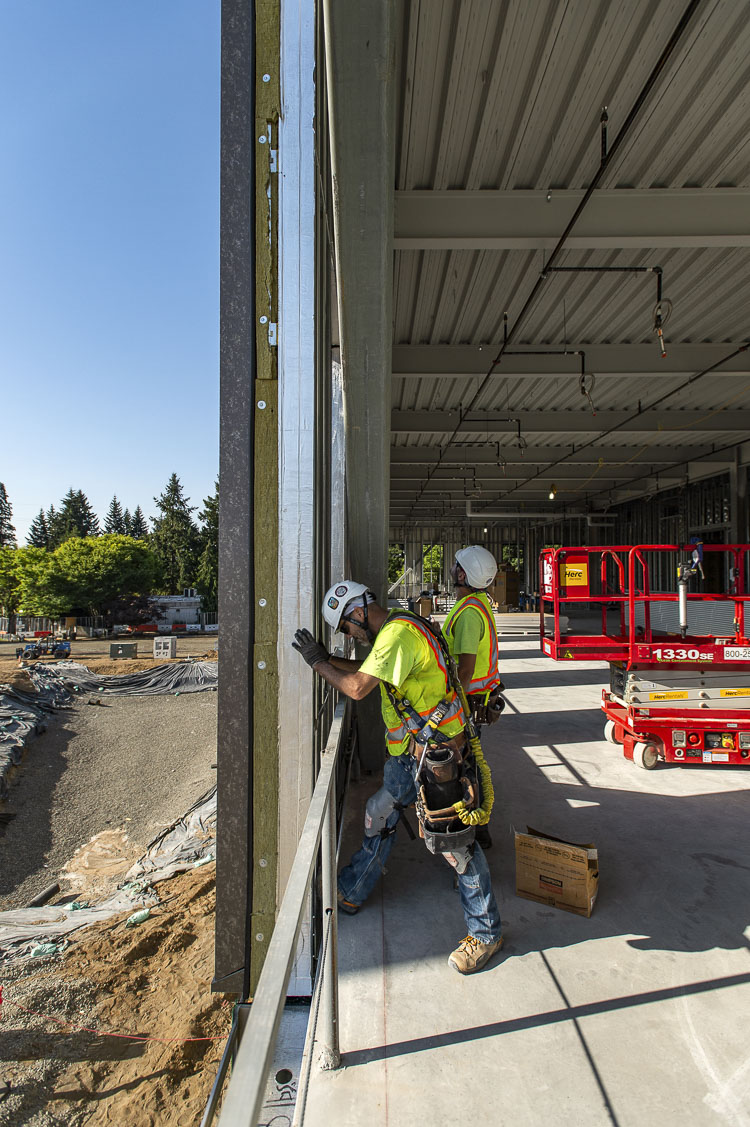
Each panel of the Ross Complex Technical Services Building project is unique. There are a series of ground floor panels that cover the first level of the building. Then a series of two-story panels up to 42 feet tall enclose the upper floors of the three-story structure. Each of these panels feature metal stud frame assembly with Swiss pearl fiber cement panels and articulated metal panels with ribs. Only specific areas were conventionally framed on the project, such as under and within structural steel canopies.
“Innovative use of prefabricated panels supported our overall design philosophy for the Technical Services Building.” said Paul Kinley, Opsis Architecture. “Our design used the color, depth, texture and pattern of the metal panel cladding to give the building a unique personality, one that responds beautifully to daily and seasonal changes in daylight. The ability to vary the application of pattern also helped express the organization of internal program areas and help communicate the mission of this important building.”
Mortenson has used prefabricated components in its projects since 2012, the most prominent example being Saint Joseph Hospital in Denver, a project that incorporated prefabricated headwalls, prefabricated bathroom pods, exterior panels and multi-trade racks. According to Rehfeldt, “the focus is always on improving the customer’s experience.”
About Mortenson
Mortenson is a U.S.-based, top-20 builder, developer, and engineering services provider serving the commercial, institutional, and energy sectors. Mortenson’s expanding portfolio of integrated services helps its customers move their strategies forward, ensuring their investments result in high-performing assets. The result is a turnkey partner, fully invested in the business success of its customers. Founded in 1954, Mortenson has operations across the U.S. with offices in Chicago, Denver, Fargo, Iowa City, Milwaukee, Minneapolis, Nashville, Phoenix, Portland, Salt Lake City, San Antonio, Seattle, and Washington, D.C. For additional information, visit www.mortenson.com.
About Opsis Architecture
Based in Portland, Oregon, Opsis Architecture serves public and private clients through designs that elevate, sustain, and inspire. The firm is focused on honing the craft of architecture to find innovative design solutions that create positive change for clients, occupants, communities, and the planet.
Learn more at opsisarch.com.
About Western Partitions, Inc.:
Started in 1972, Western Partitions has grown to become one of the largest interior and exterior contracting firms in the western U.S., providing numerous services to its clients. Constructors bring their expertise to the table every day with innovative thinking, building safely, and building efficiently.
Learn more at https://wpibuilds.com/
About Bonneville Power Administration
The Bonneville Power Administration is a nonprofit federal power marketer that sells wholesale, carbon-free hydropower from 31 federal dams in the Columbia River Basin. BPA delivers this power to more than 140 Northwest electric utilities, serving millions of consumers and businesses within its service area. BPA also owns and operates more than 15,000 circuit miles of high-voltage power lines and 261 substations, and provides transmission service to more than 300 customers. In all, BPA provides nearly a third of the power generated in the Northwest. www.bpa.gov
Also read:
- Opinion: Schools notifying parents about the kinds of care kids can decide on their own didn’t make itElizabeth New criticizes the removal of Amendment 1164 from current legislation, arguing it leaves parents uninformed about health care services accessed by their children through schools.
- Ridgefield School District invites community to help shape new Strategic PlanRidgefield School District is hosting three public sessions to gather community input for its new Strategic Plan.
- Julianne Lawrence is first paid director of Two Rivers Heritage MuseumJulianne Lawrence has been appointed the first paid director of the Two Rivers Heritage Museum following a strategic effort by the Camas-Washougal Historical Society.
- Foundation for Vancouver Public Schools breaks ground on new building to support construction trades at Fort Vancouver High School with the Ed and Dollie Lynch FundFort Vancouver High School will soon be home to a donor-funded trades center focused on welding and advanced manufacturing education.
- Save Vancouver Streets has its day in court, waits on rulingSave Vancouver Streets went to court to argue that the city must allow its initiative to proceed after collecting more than 6,500 signatures.
- Opinion: Off-road vehicles in the neighborhoodDoug Dahl responds to a resident’s concern about off-road vehicles on neighborhood streets, outlining the legal violations and safety risks involved.
- IBR only has single firm interested in managing the project to replace I-5 BridgeRep. John Ley reports on serious concerns with the I-5 Bridge replacement project, including limited contractor interest, rising tolls, and a 15-year timeline.